Can BladeTracker and drones be complementary?
BladeTracker can provide full coverage blade inspections, this article was written for a special case:
The BladeTracker technology differs from drone inspections as it is a ground based system positioned near the base of the turbine tower. Therefore, by definition, it inspects from a larger distance than drones do. The benefit however is that the turbine does not need to be shut down during a blade inspection as the BladeTracker is capable of following the motion of the rotor whilst capturing images. We often get the question whether the resolution of our images meets the resolution of drone images. In many cases, due to the hardware we use, we can. In some cases not. It also depends on the drone company used and the equipment they use. However, in some cases this question is less relevant. Some customers understandably like to stick to drone inspections. For these, we are proposing an alternative business case where we can achieve a considerable cost reduction. BladeTracker is used as a selecting tool: we inspect an entire windfarm without shutting down one single turbine. Based on the reporting our client can then decide which turbines require a closer inspection (if necessary at all) or to directly move to repair through rope access. This reduces the overall shutdown time of the wind farm drastically.

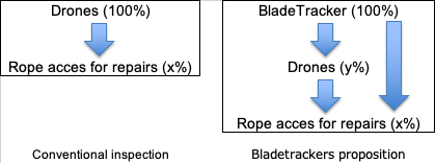
Interested in this concept or want to share some thoughts? Feel free to contact us!